Compact Double Block & Bleed vs. Conventional Installations
Facts about the Conventional Installation
Double block and bleed valve systems are conventional installations for most End-Users in the Oil and Gas industry. Conventional installations of DBB valve systems have become a normal practice and can even be found on offshore platforms.
The installation of DBB valve systems is a time consuming process that can negatively impact employees and their work production. The normal process of this type is baded on:
- Using two 6” 1500 class ball valve with all the additional materials,
- Long and comlex installation process (up to a 41 steps)
- Huge amount of material (weight of 2,645 lb(s) = 1200 kg)
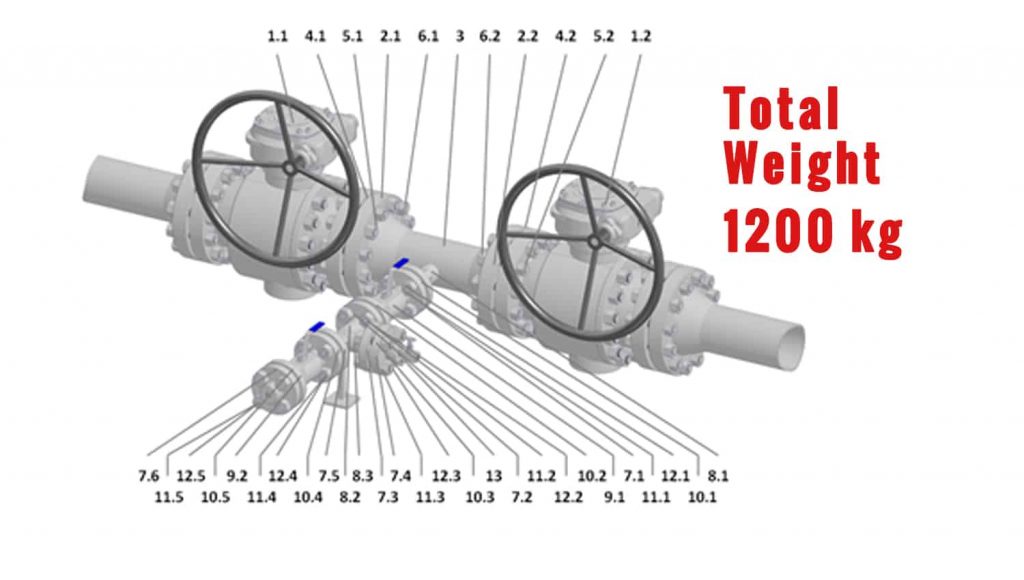
Pros of the Compact Double Block & Bleed Valve solution
In comparison, a prefered method is to use a Compact DBB Valve and not doing a conventional installation with individual valves.
Instead of using two valves in the earlier example, Compact Double Block & Bleed Valves only requires one single valve. This results in:
- Reduced weight (down to 2,094 lb(s) = 950 kg) –> If the end-user has 10 different DBB valve installations, using Compact DBB Valves would eliminate over 20,000 extra pounds of weight
- Increasing profits because of minimized shut down time
- Highest safety with maximizing customer profits
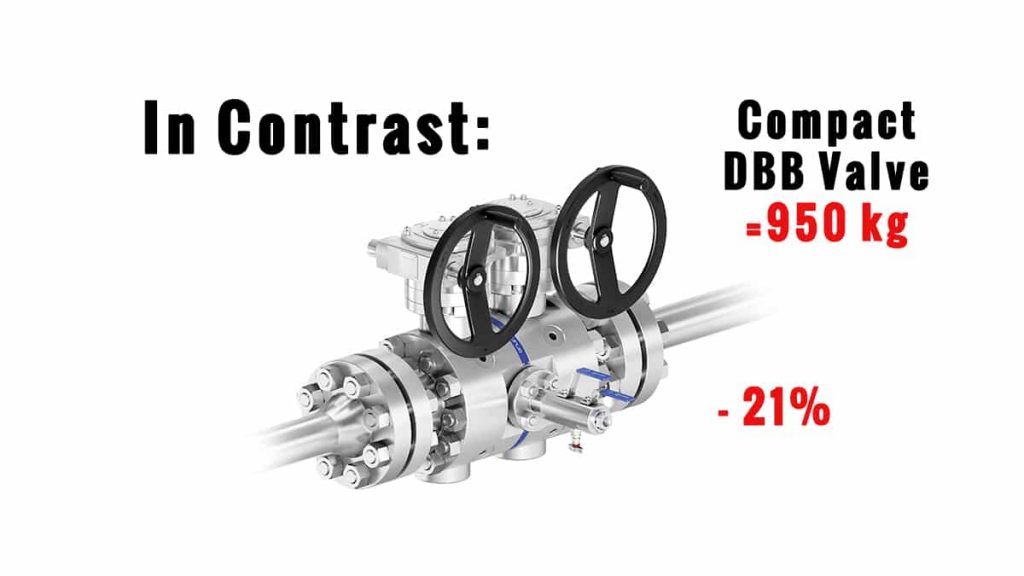
(Images source: © Sergey Ilin/Fotolia, Alexander Potapov/Fotolia)