DBB Valves: Floating vs. Trunnion Ball Design
Lately I was often asked about the difference between a floating and a trunnion ball valve. Well, I try to explain it in a few words without going to deep into the technical details. This would be too much for this post.
Status quo Ball Valves
- In the closed position, the ball has to seal the medium against the medium pressure
- The sealing elements are the ball and the valve seat
- The Ball is usually made of steel, the seats usually are made of plastic or also metal
- For having a tight shut-off, the sealing elements (ball and seats) have to be pressed together
- This compression is done by a preload of the seats and also the system pressure
- The higher the pressure, the higher the forces which presses the sealing elements together
Problem
The higher the pressure, the more the sealing elements are pressed together – and the higher are the forces on the ball and the seat.
This would not be a big problem, if the valve has not to be operated like a check valve. But a ball valve has to be operable, even under high differential pressure.
When high forces are acting on the sealing elements, the friction between them is high. This means that the operation torque and the wear on the parts are also high.
If you only look on the high operating torque, you could take measurements like very long handles, or a gear.
But the length of handle is limited in design standards like ISO14313 / API 6D, because it causes other problems like collision with other piping elements and a gear is expensive.
You can also reduce the operating torque by reducing the friction coefficient of the material pair, i.e. by using modified plastics (PTFE-filled PEEK). But the reduction of the operating torque is not always as high as you need.
You also have to look on other things like wear of the sealing elements, with respect on the lifetime of the valve and also on the dimensioning of the stem. Big stem diameters have the consequence that also other parts like the body need to be bigger and so the cost of the valve will increase.
⇒ A reduction of the operating torque and the forces on the sealing elements is very important, especially for higher pressures.
Solution
But how to reduce the forces on the sealing elements?
Using a trunnion ball design instead of a floating ball design.
What’s the difference?
Formula for the force applied on the sealing element:
F = p x A
F = Force
p = pressure
A = Area on which the pressure is applied
⇒ As the pressure is given, you have to reduce the size of the area.
Floating Ball
- The valve seats are fixed in the valve body
- In the closed position, the ball can move a little bit in flow direction
- The ball is pressed against the downstream seat
- The system pressure acts on the whole circular area of the ball
⇒ Big Area = Big Force
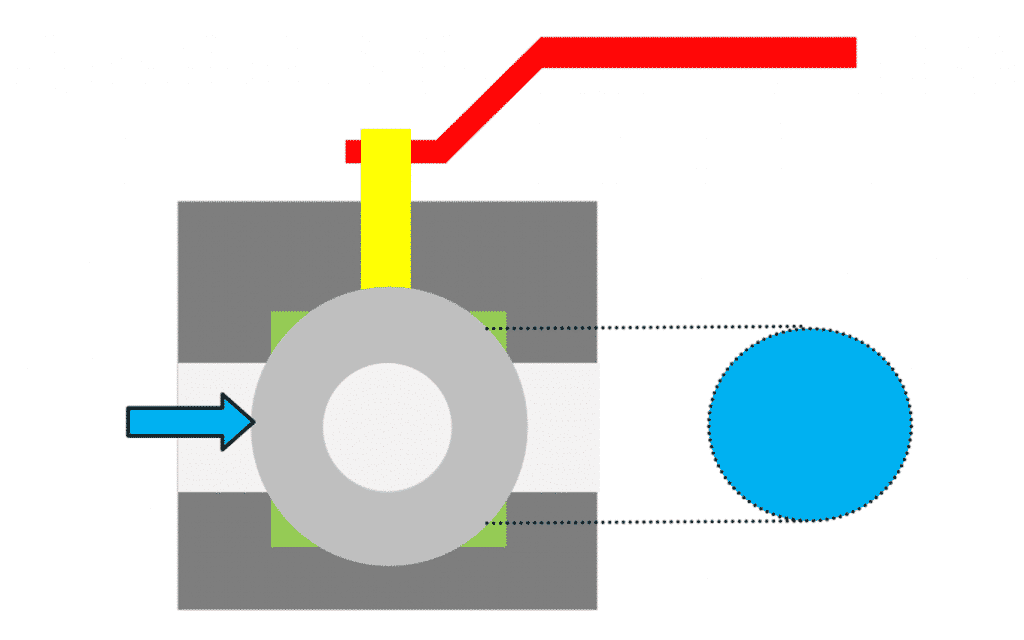
Trunnion Ball
- The ball is fixed in position by trunnions (bearing) and can only rotate
- The seats can move a little bit in flow direction
- The upstream seat is pressed against the ball
- The system pressure acts on the circular ring of the upstream seat
⇒ Small Area = Small Force
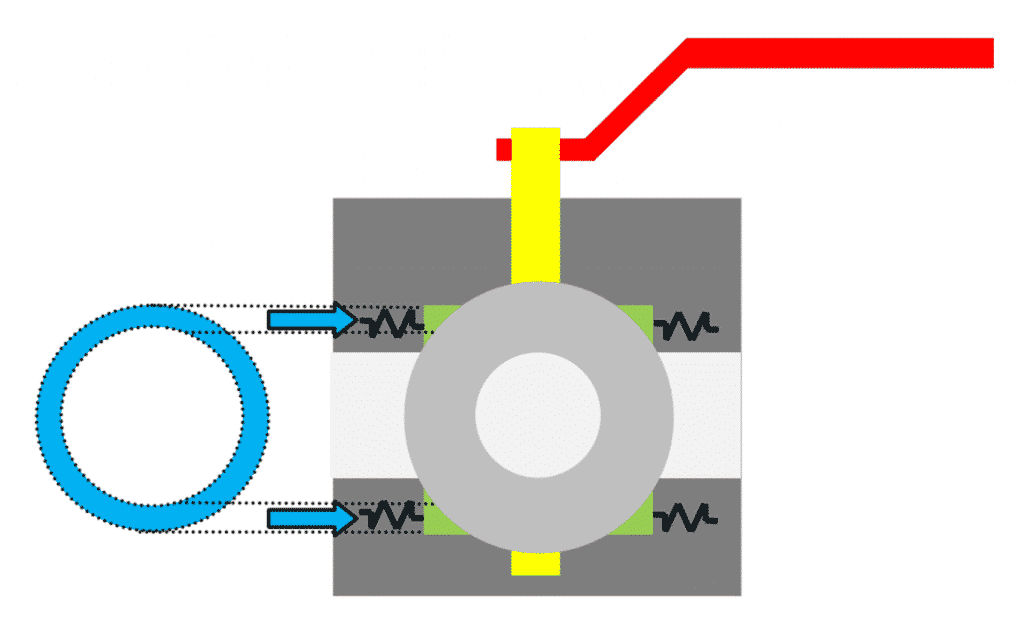
Remark: As this sketch is only for illustration, please ignore the wrong orientation of the handle (this should be transverse to the flow direction).
Advantage Trunnion Ball Design
You can list all the advantages of a trunnion ball over the floating ball:
- lower operating torque
- less wear on the ball and the valve seats
But why not using the trunnion ball in general?
Well there is a significant disadvantage: You need more components and this has an impact on the costs.
Therefore you have to decide well, which design you use.
But how to decide?
Standards like EEMUA 182 give rules, when to use the trunnion ball design:
- For Class 150 and 300 à DN 150 (NPS 6) and higher
- For class 600 to 2500 à DN 50 (NPS 2) and higher
Also customer specifications give clear rules, when to use a trunnion ball design, depending on the pressure class and the bore size.
My Opinion
For small bore sizes there is no need for a trunnion ball. Trust the valve manufacturer, as he should have tested the different pressure class and bore size combinations and decided for the right design.
AS-Schneider offers as standard:
- Floating ball design: DN 25 (NPS 1) up to DN 50 (NPS 2)
- Trunnion ball design: DN 50 (NPS 2) and bigger
As you can see, only for the DN50 (NPS 2) size, you have the choice whether you want to have a floating or a trunnion ball. In my opinion you should decide for a trunnion starting with class 600.
(Images source: © AS-Schneider)