“Fire Safe Approved” vs. “Fire Safe by Design”
During the last years I recognized, that people sometimes talk about “Fire Safe by Design“. When I was coming across this the first time, I wondered about the meaning of this in detail – Just using metal to metal sealing, graphite sealing or graphite packing?
“Fire safe by Design” is widely used, but to my knowledge there is no common or firm description or rules limiting or qualifying the use of this concept.
Let’s say we can talk about a scale of 3 levels:
- Top-level
- The Valve is Fire Safe tested and approved according to common standards like API 607, API 6 FA, ISO 10497, etc., or the valve is within the qualification range of this standard.
- This means it has been pressurized, set under fire at a defined temperature and duration and after stopping the fire supply the valve has been shock-cooled and the leakage is below a given limit.
- Mid-level
- Similar to Top level, but this valve has not been tested. The same valve design has been Fire Safe tested and approved, but the valve is outside the qualification range of the standard
- in Carbon Steel not in Alloy 625
- the valve size is one size outside of this qualification range
- with PTFE seats, not with POM seats
- etc.
- Example: Valve of same design has been tested and approved, but:
- This is usually for economical or time-consuming reasons, or because the standards do not include the sizes or pressure classes.
- It’s up to the customer/end user to accept this argumentation
- Similar to Top level, but this valve has not been tested. The same valve design has been Fire Safe tested and approved, but the valve is outside the qualification range of the standard
- Low-level
- The Valve design has not been tested, not even a similar one, or there are large deviations in design in comparison to an approved one (e.g. Floating ball valve has been approved and should also qualify a trunnion ball valve).
There is a big risk when accepting the low-level Fire Safe design, especially when no tests have been done at all.
Risk of untested valves, even if the design can be expected to be fire safe
I want to share my experience during a Fire Safe test/approval of our Double Block and Bleed (DBB) Monoflanges:
An AS-Schneider Monoflange consists of the valve body and 3 Needle Valves for isolating and venting the medium. Each valve we develop is tested extensively in our “TechCenter” to be sure that all requirements of our customers are met. Also in case of a fire safe approval we do pre-tests in our fire safe test rig, before we order the third party for witnessing. For the Monoflange approval I was very confident that we will pass the test at the first trial, because we only use metal to metal sealing and graphite packings – but then there was a great surprise: The valve seat was leaking during the heating period.
The reason therefore was that the valve tip was lifting from the valve seat, as the parts directly exposed to the flames where expanding faster than the parts inside the valve (stem and tip). Although all parts are made of the same material and therefore have the same thermal expansion coefficient, there was a difference in increase of length for different parts (see also cross section below).
The solution was the to use a special spring-loaded design to compensate the different thermal expansion and keep the valve tip pressed into the valve seat – this is now the standard for OS&Y head units. As a positive side effect, the spring-loaded design provides also a live loading to the packing which ensures tightness also during non-critical operating conditions.
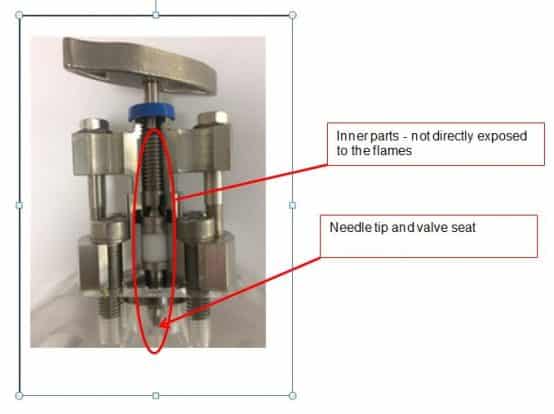
This OS&Y head unit is not only installed on our Monoflange, but also as a vent valve on our DBB Taurus Series (Double Block & Bleed Pipeline Ball Valves). The Taurus Series has also been fire safe tested and approved, using this OS&Y head unit as a bleed valve.
(Image source: © AS-Schneider)